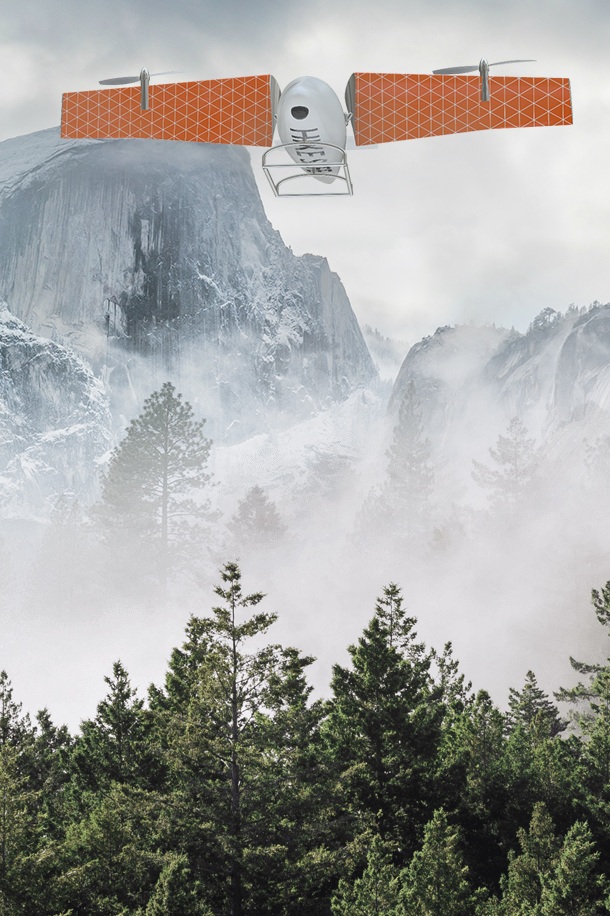
HikeSafe
Provide safety, security, and rescue to lost and injured hikers through automation and robotics
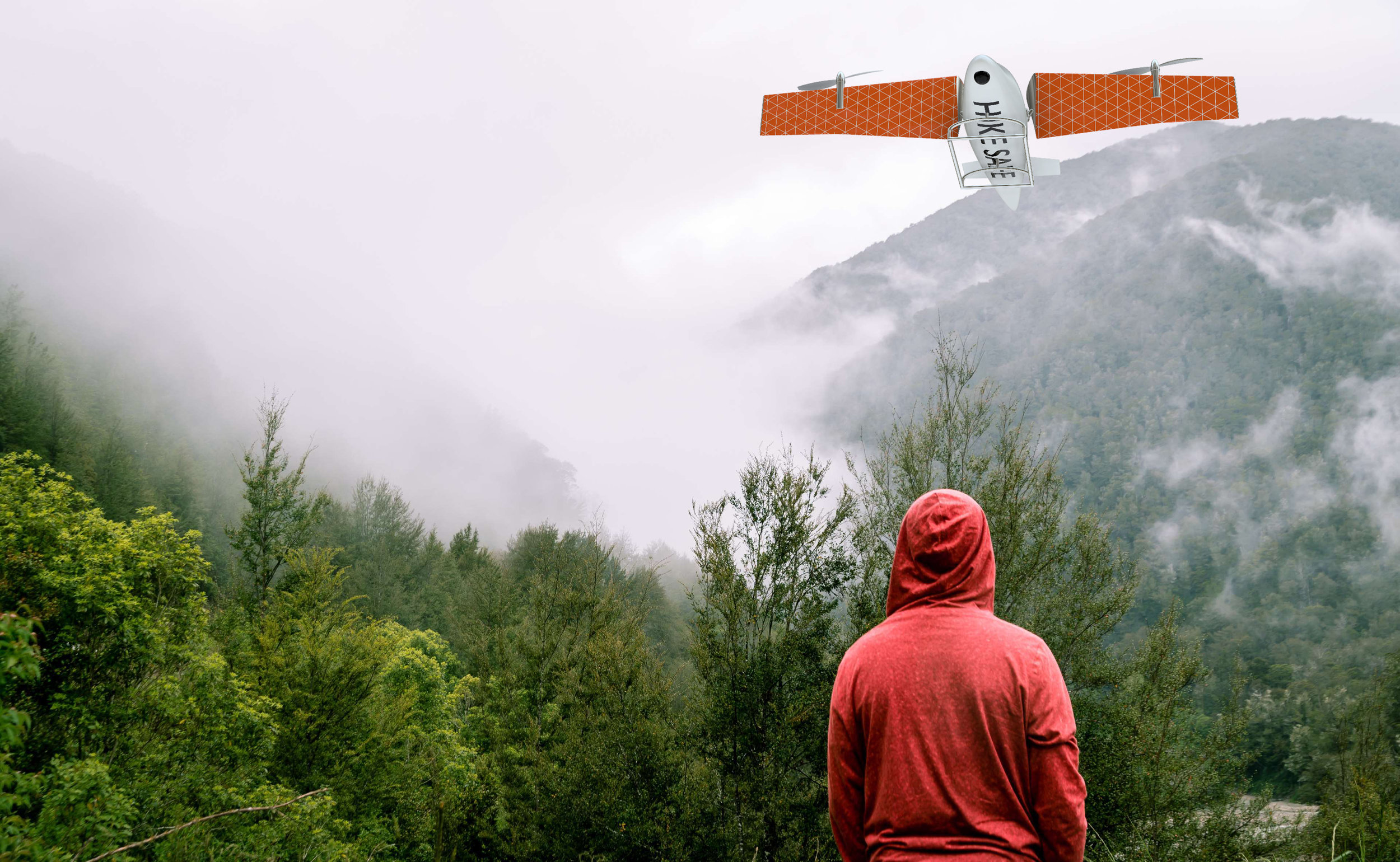
OVERVIEW
CLIENT:
Student Project for Product Design Course
PROCESS:
Qualitative and Quantitative Research , User Personas, Sketching, Cardboard Prototyping, Low-High Fidelity Concept, 3D Modeling and PrototypingROLE:
Researcher and Designer for HikeSafe DronePARTNERS
Ivan De la Rosa and Mordechai Freedman
Problem
Through our research, we discovered that a typical search and rescue operation takes an average of 9 hours before a person is found. With an average cost of $1700 per hour on helicopters Search and Rescue Operations add up to hundreds of millions of Taxpayer dollars per year alone. The wilderness is vast, massive, and often unpredictable. Locating people can quickly become an arduous task even for the most experienced SAR Rangers. With HikeSafe we seek to reduce Search and Rescue response time, with the goal of saving more lives.
Goal
● Reduce response time to lost or injured hikers
● Deliver immediate first aid
● Expedite Search and Rescue (SAR) operations
● Immediate feedback on hikers whereabouts and health status
Exploration Sketching
Sketching allowed me to rapidly explore possible directions to which I could prototype a rescue drone based on preliminary user requirements. The drone had to be large enough to deliver essential rescue items quickly. Therefore, it took shape from an airplane, but to land safely without a runway, it needed to land and take off vertically. I took inspiration from the United States Marine Corp V-22 Osprey which is used to transport Marines quickly in tight spots without the use of runways.
Cardboard Prototyping
Using the corrugated fiberboard cardboard allowed me to build a strong enough wing for it not to sag. It was cheap and fast to make compared if I had to use other materials such as metal, wood or plastic. I started off by making precise measurements of the cuts to be made and used a standard box cutter to cut out the pieces to be assembled carefully. Plenty of hot glue was used as well as patience. Based on feedback the drone needed to be more aero-dynamic and be more prominent to carry onboard systems such as an infrared camera to include rescue kits to be lowered or dropped to lost hikers.
Refine and Design
Using feedback received in class and from hikers, I began to refine my drone’s concept direction. The next step was to use Autodesk Fusion to start modeling the drone. This was a big challenge for me since I had no prior experience using CAD software. However, having a pre-template drone allowed me to save time by modifying its shape and form based on my concept. I began with low-fidelity models of my drone in Fusion and continued to make iterations based on feedback. I then started to prepare to model the propeller in preparation for 3D printing. The propeller was 3D printed from PLA which made it less expensive than ABS. 3D printing inspired me to the possibilities of creating real-life products from research in a short period. Also, printing the propeller provided me with a sense of scale for the drone and feedback from my peers. Feedback from my peer and experts influenced the color of the drone to orange and white for better visibility in fog or rainy conditions.
High Fidelity and User Testing
The high-fidelity prototype is a rendered branded model of the drone. It was used to conduct user testing as a group and to evaluate my design. A scenario was created through story-telling in which users provided details as to their user requirements from being rescued. User testing through storytelling was a challenging task because it is not conventional for a product design course. However, the research proved to guide the concept to a product that full-filled user requirements.